Dây chuyền chiết rót chất làm bóng gương đóng túi đóng vai trò quan trọng trong việc tạo ra thành phẩm đáp ứng nhu cầu thị trường. Ứng dụng của dây chuyền còn mở rộng sang nhiều lĩnh vực khác như hóa chất, mỹ phẩm, thực phẩm,… Với khả năng tự động hóa cao, mỗi công đoạn đều được thực hiện một cách chính xác và nhanh chóng nhờ vào sự hỗ trợ của các thiết bị hiện đại như máy bơm, máy chiết rót, máy đóng gói và dán nhãn tự động. Ưu điểm nổi bật của dây chuyền chính là khả năng linh hoạt trong việc điều chỉnh các thông số kỹ thuật, đáp ứng đa dạng các yêu cầu của khách hàng. Bên cạnh đó, dây chuyền còn đảm bảo vệ sinh an toàn thực phẩm, tuân thủ các tiêu chuẩn chất lượng quốc tế.
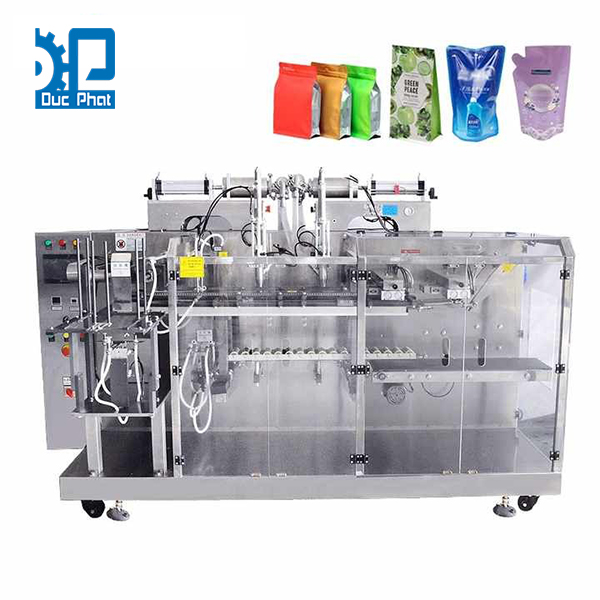
Thông số kỹ thuật
Loại bao bì | Túi đứng, Túi zip, Túi sẵn |
Kích thước túi | 100mm<Chiều rộng>300mm, 100mm<Chiều dài>420mm |
Tốc độ | 15-20 túi/phút |
Cân nặng (KG) | 500 |
Ứng dụng | Thực phẩm, Đồ uống, Hàng hóa, Hóa chất |
Điện áp | Điện áp xoay chiều 220V |
Kích thước (D*R*C) | 1635*510*1650mm |
Tiêu thụ khí đốt | 0,5 cm³/PHÚT |
Loại máy | Tự động |
Xuất xứ | Trung Quốc |
Hình ảnh máy trong dây chuyền
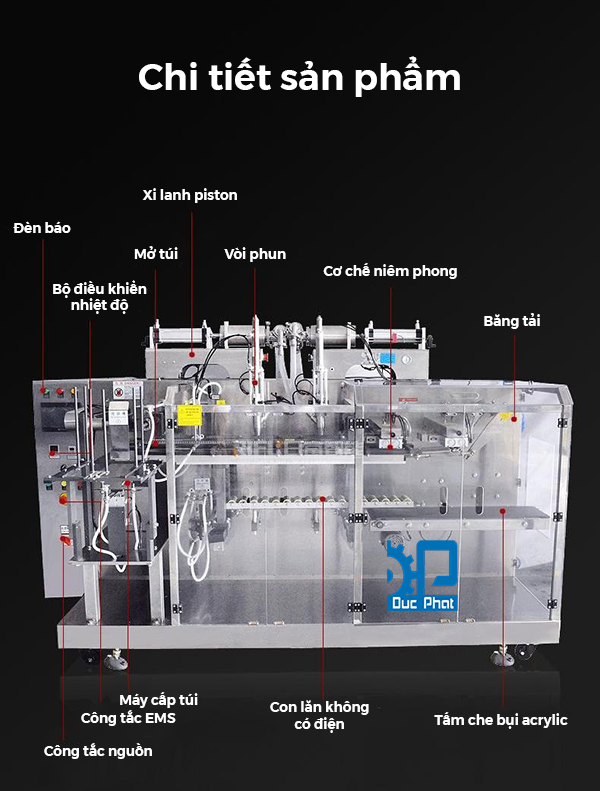
Các bước chiết rót
Bước 1: Chuẩn bị nguyên liệu
Nguyên liệu được pha chế theo công thức được nghiên cứu và thử nghiệm kỹ lưỡng. Các chỉ số quan trọng như độ nhớt, màu sắc, và tính ổn định hóa học được kiểm tra bằng thiết bị chuyên dụng. Sau khi hoàn thành các bước kiểm định, chất làm bóng gương được nạp vào bồn chứa trung tâm của dây chuyền. Hệ thống bơm chuyên biệt đảm nhận việc đưa nguyên liệu vào bồn lưu trữ, sẵn sàng cho các khâu tiếp theo trong sản xuất.
Bước 2: Định lượng, chiết rót
Hệ thống định lượng thông minh vận hành tự động, sử dụng cảm biến để đo lường lượng nguyên liệu. Từng túi được chuẩn bị sẵn tại vị trí chiết rót sẽ được cấp một lượng chất làm bóng gương đúng theo thông số đã cài đặt. Nhờ điều chỉnh linh hoạt tốc độ dòng chảy và áp lực bơm, sản phẩm không bị tràn hoặc xuất hiện các hiện tượng như tạo bọt hay không đều về khối lượng.
Bước 3: Hàn kín túi
Miệng túi được xử lý bằng công nghệ hàn nhiệt cao cấp, tạo ra mối liên kết chắc chắn và bền vững. Các túi vừa niêm phong được đưa qua một bộ phận kiểm tra đặc biệt, nơi cảm biến sẽ phát hiện các lỗi như rò rỉ hoặc không đạt tiêu chuẩn. Việc này giúp sản phẩm sau khi niêm phong luôn ở trạng thái an toàn tuyệt đối, hạn chế tối đa tình trạng hư hại trong khâu vận chuyển.
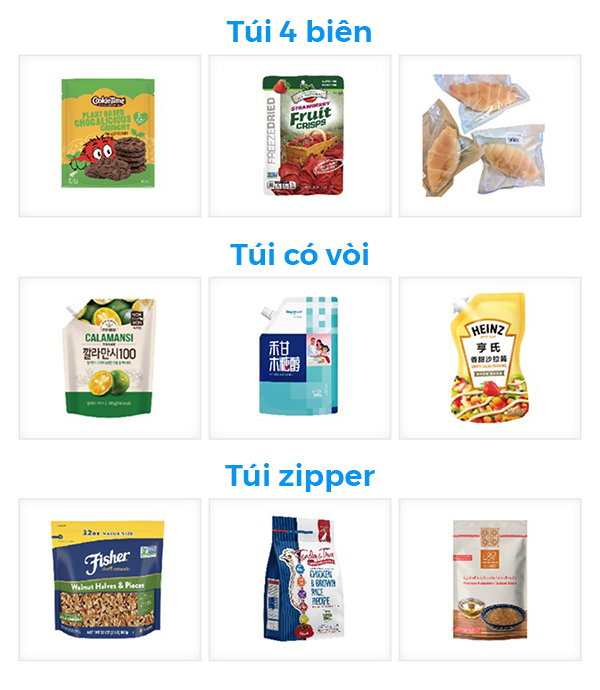
Bước 4: In thông tin và hoàn thiện
Máy in phun hoặc hệ thống dán nhãn tự động thực hiện việc ghi thông tin chi tiết lên từng túi, bao gồm tên sản phẩm, dung tích, số lô sản xuất, và hạn sử dụng. Sau đó, các túi được kiểm tra lại để loại bỏ những sản phẩm không đạt yêu cầu về độ thẩm mỹ hoặc thiếu thông tin. Tất cả đều được vận hành theo một chuỗi khép kín, giúp từng sản phẩm hoàn chỉnh đạt được tiêu chuẩn về hình thức lẫn chất lượng.